A Turning Point For Biopharmaceutical Industry
We provide complete design, engineering, construction, start-up of new pharmaceutical facilities, even assisting the Clients through scouting activities of potential Know How Licensor, transferring the Know How, providing Validation Master Plans and Standard Operating Procedures, validating, aligning industrial processes to URS and regulatory requirements.
ZHM Proposes Reliable Know-How & Technologies About:
- LVP (Large Volume Parenterals) in PVC or PP bags
- LVP in Glass or Plastic Bottles
- SVP (Small Volume Parenterals) in Glass or Plastic Vials and Ampoules
- Pre-filled Syringes
- IV products (bags, glass and plastic bottles)
- Blood bags (LVP bags in PVC)
- Dialysis concentrate solutions and powders (Canisters, Bags, Cartridges)
- Plasma Fractionation
- Biotechnological Plants
- Multipurpose Pharmaceutical Plants
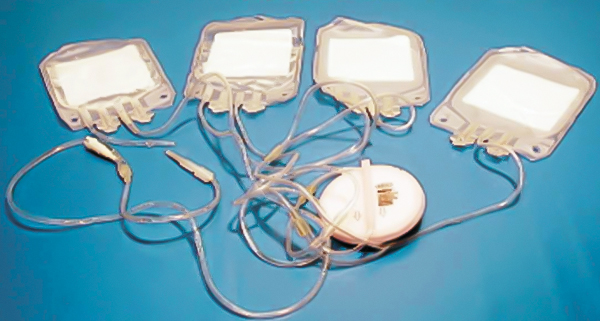
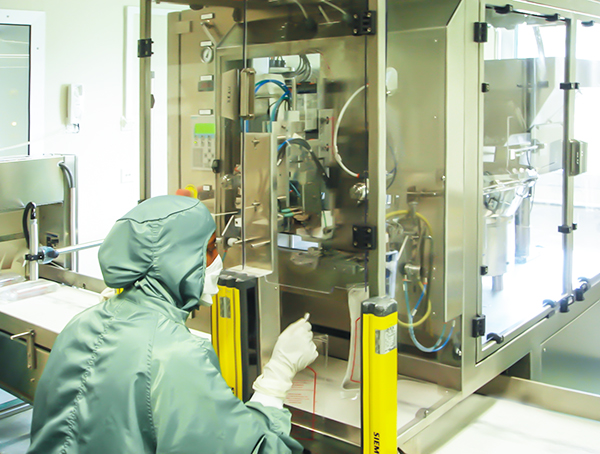
- Procurement of Licensors and Know How Transfers
- Conceptual Design and Design Qualification (DQ)
- Detailed Engineering
- Validation Master Plan & S.O.P.
- Equipment Construction & Procurement
- Factory Acceptance Test (FAT)
- Shipment and Installation
- Site Acceptance Test (SAT)
- Standard & Validation Documentation (IQ/OQ/PQ Protocols)
- Training
- Commissioning, Calibration & Start up
- Regulatory Support
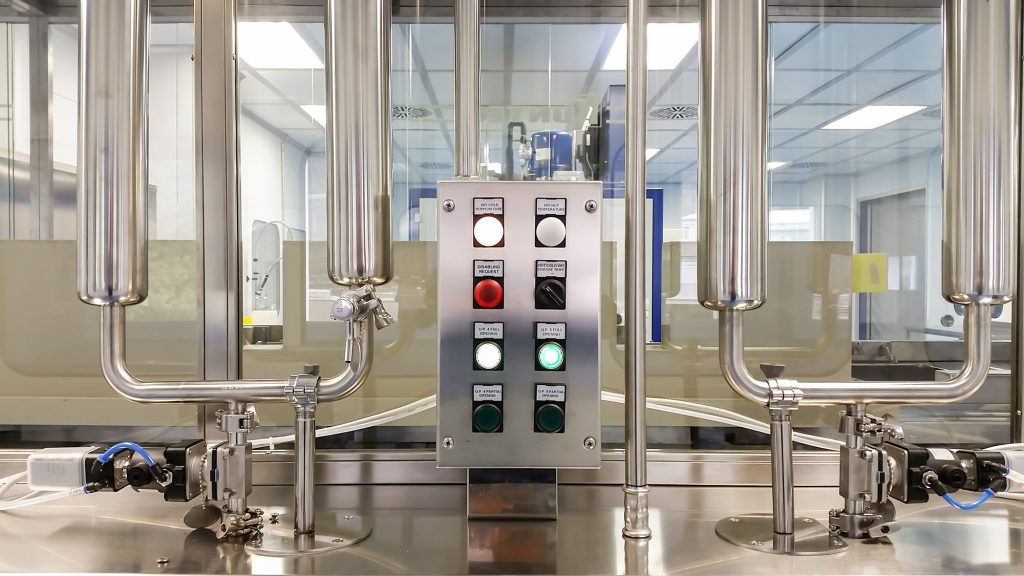
ZHM provides complete design, engineering, construction, start-up of new pharmaceutical facilities, even assisting the Clients through scouting activities of potential Know How Licensor, transferring the Know How, providing Validation Master Plans and Standard Operating Procedures, validating, aligning industrial processes to URS and regulatory requirements.
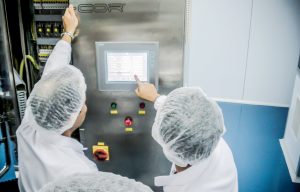
The necessary training for operation and maintenance of the lines is provided by our expert technicians at the system start-up, ensuring a full understanding of how the equipment works and how to operate for effective sanitization/sterilization and troubleshooting. Different training for different access levels to the system is taken into account and recorded on ZHM certificate of attendance. Action options and limitations for the End-User, which are diversified according to the access level, are clearly highlighted during training.
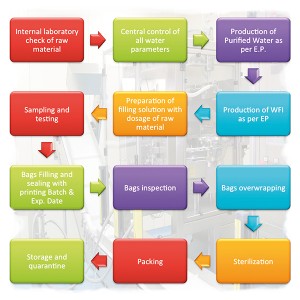
We propose reliable turnkey know-how, engineering and services about:
- LVP (Large Volume Parenterals) in PVC or PP bags
- LVP in Glass or Plastic Bottles
- SVP (Small Volume Parenterals) in Glass/Plastic Vials/Ampoules
- Pre-filled Syringes
- IV products (bags, glass and plastic bottles)
- Blood bags (LVP bags in PVC)
- Dialysis concentrate solutions and powders(Canisters, Bags, Cartridges)
- Plasma Fractionation
- Biotechnological Plants
- Multipurpose Pharmaceutical Plants
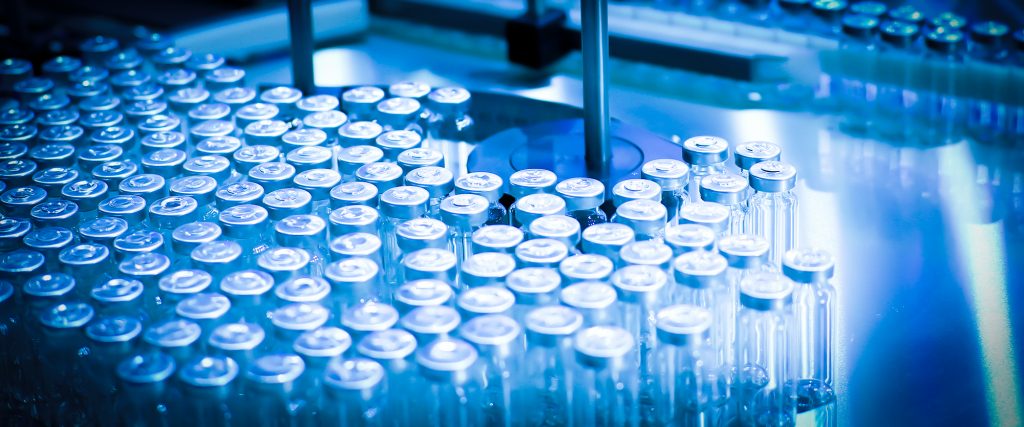
ZHM engineering team focuses mostly on fluid drugs sterile production processes. A full understanding of the drug production process is the key concept for correct design, born from almost 50 years of experience. Clear definition, assessment, monitoring of critical parameters directly affecting product quality are the baseline for the application of suitable Process Analytical Technologies granting both complete in-line and at-line quality control. Every process follows rigorous cGMP-compliant Standard Operating Procedures. Specification, construction, verification steps within the project lifecycle follow GAMP “V” models, considering Risk Assessment, architecture of system components, functional specification, sanitization, sterilization and validation issues with special overview to a sustainable maintenance of the system. Our ZHM work breakdown structure consisting in following activities:
- Design (quality by design)
- Construction (mechanicals, electro-pneumatics, software)
- Testing
- Documentation
- Installation
- Validation
- Start up
A complete technical documentation is part of our equipment and includes:
- General Documentation and Constructive Specification
- Components Documentation
- Valves Documentation Instruments Documentation
- Electrical/pneumatic Documentation
- Hardware and Software Documentation
- Piping, Fitting and Welding Documentation
- Non-destructive test certificate
- Operating and Maintenance Instructions
- Spare Parts
ZHM involves its proven experience in three ranges of pharmaceutical equipment:
Water Treatment Systems
ZHM pharmaceutical water treatment systems are designed to produce compendial
PW – Purified Water
HPW – Highly Purified Water
WFI – Water For Injection
PS – Pure Steam
Pre-treatment options, monitoring of critical parameters, regulatory requirement for product quality, consumptions, microbiological control, operation and maintenance requirements, lifecycle costs are key points in our design of all processing steps, from feed water to the point of use. Special care is given to the choice of sanitary materials. Product-contact surfaces are in certified AISI 316L stainless steel, with standard roughness ≤ 0.4 µm. EPDM or PTFE gaskets ensure perfect sealing. Advanced Process Analytical Technologies are applied for monitoring issues and professional GAMP compliant automation is provided for system control.
PROCESSING SYSTEMS
ZHM designs, manufactures and installs complete Formulation & Preparation Plants starting from specific Product and User Requirements. Sterile preparation or cleaning and sterilization of process vessels or contact equipment are common issues in the pharmaceutical industry and therefore a must in any of our projects. Specific manufacturing of solutions or sanitization & sterilization requirements can be satisfied by our processing systems, providing the optimum balance of performance with cost effective aseptic processing equipment through ZHM solutions including:
Mixing Tanks And Bioreactors
Mixing Vessels
Pressure Tanks / Pressure Vessels
Reactors Vessels
Customized Formulation Tanks
Mobile Mixing Vessels
Atmospheric Transfer Tanks
Cip/Sip Systems
Customized Stations
Mobile Stations
Ancillary Systems For Formulation Lines
Triblenders
Filtration Groups
Solution Transfer Circuits Through Nitrogen Or Sanitary Pumps
Vessels Loading Platforms
Laminar Air Flow Cabinets
ZHM pharmaceutical bags or bottles filling equipments are intended for automatic, semiautomatic or manual use, for different bags or plastic/glass bottle sizes, according to various production needs from min. 10 ml, smaller volumes on demand. Our equipments ensure trouble-free operation, with reduced maintenance costs and long-term reliability. Complete bottle lines are integrated with washing machines, capping and crimping machines, labelling lines and belt conveyors.
Manual, Semiautomatic and Automatic Filling Machines for BAGS
BAGS making machines
FORM-FILL-SEAL equipment for PP BAGS
Visual Inspection lines for BAGS
Machines for assembling Plugs and Connectors for BAGS
Filling Machines for BOTTLES
Washing, Stoppering, Capping Machines for BOTTLES
STRETCH-BLOW-MOLDING Machines for PP BOTTLES
Complete integrated lines including CIP /SIP skids
Professional Installation
Professionalism in installation is a basic requirement in all pharmaceutical technologies. We provide installation teams composed of qualified supervisors, patented welders and skilled piping assemblers working in accordance to ZHM sanitary piping procedures all over the world.ZHM water treatment equipments are thus integrated to state-of-the-art, GMP-compliant distribution systems, which are inspected during construction, passivated and tested. Isometric drawings of the “as built” loops are supplied as part of the loop documentation, together with the relevant material certificates.
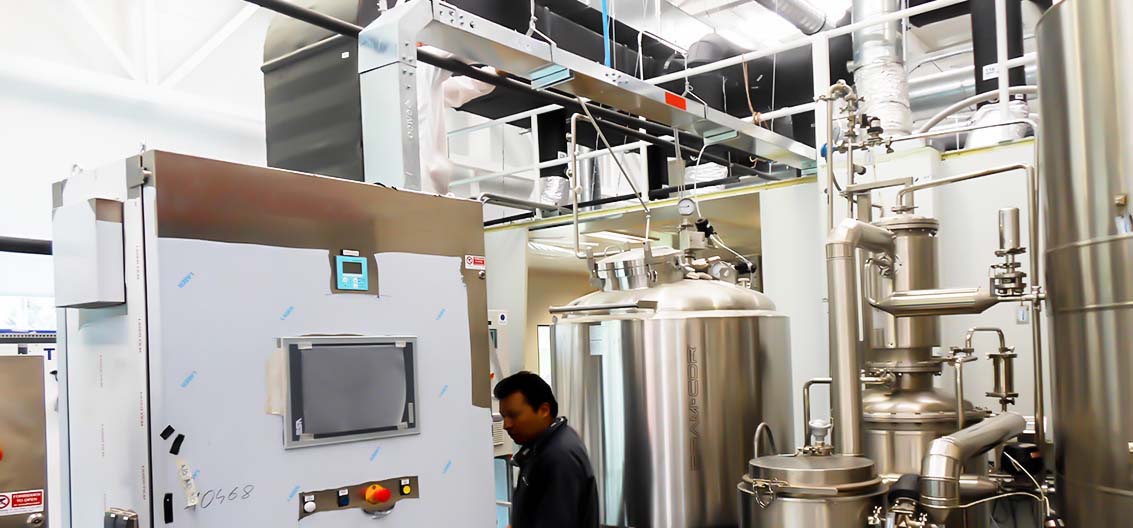
Full Services
Top quality cGMP equipment must necessarily be integrated through a proper high level of professional services including:
- Technical Documentation
- Factory Acceptance Test
- Endotoxin Test
- Installation (see related page in this site)
- Commissioning, Site Acceptance Test & Start-up
- Training
- Validation
Our worldwide network of skilled agents and our affiliated companies ensure assistance to our Clients in over 50 countries, from the very beginning of a pharmaceutical project throughout decades after start-up. ZHM After Sales Dept. grants punctual and quick deliveries of spares and ongoing technical support.
Engineering & Technical Documentation
All Pharmaceutical Facilities need to be up-dated, competitive and efficient in operation, to diversify production programs, to reduce life-cycle costs and, above all, to comply to the appropriate pharmaceutical GMP regulation. ZHM project drivers are aimed at satisfying all pharmaceutical regulatory and QA requirements, aligning the final product to the international Pharmacopoeias and capitalizing upon a careful, customer-oriented project management. Equipment and process flow are designed to allow a logical flow in order to avoid mix-ups of components, drug product, closures, labeling, in-process materials or cross contamination achieved through the development of
- Conceptual Design describing the general project organization
- Detailed Engineering, considering all process flows (raw materials, finished products, personnel, waste, etc.) and detailed project specifications
A complete technical documentation is part of our machines and includes:
- General Documentation and Constructive Specification
- Components Documentation
- Valves Documentation
- Instruments Documentation
- Electrical/pneumatic Documentation
- Hardware and Software Documentation
- Piping, Fitting and Welding Documentation Non-destructive test certificate
- Operating and Maintenance Instructions
- Spare Parts
During the initial phases of the process we assist our Clients with a feasibility study and an engineering support due to optimize the entire project from the overall investment point of view, considering operational costs reduction. In case of Critical Fluids Systems (PW, WFI, PS), we usually ask to provide us with following basic data:
- Raw water analysis
- Table of concurrent uses in the 24 hours (ask for more information)
- Lay-out with location of each user point, as well as of the equipment (we are ready to assist the Clients in defining the most suitable layouts)
Through our software we can perform all necessary simulations and recommend the best solutions. Either counting or not on our initial engineering support, we provide a complete set of specifications in our DESIGN QUALIFICATION protocols, which are submitted to our Customer for approval before starting the equipment construction.
Commissioning includes factory testing, site testing and start-up activities, ensuring that the system is correctly running and that the final product meets all specified requirements within the operating range.
ZHM systems are first pre-tested in our facility, tested in the presence of the Customer during FAT, and finally tested on site (SAT) under real operating conditions by professional and competent ZHM technicians. Product critical parameters are carefully monitored, as well as fluid flows, pump duties, alarms, valves, emergency power and software modules. Our FAT and SAT protocols provide a complete documentation of testing activities.
Training Of The End-User
The necessary training for operation and maintenance of ZHM pharmaceutical systems is provided by our expert technicians at the system start-up, ensuring a full understanding of how the equipment works and how to operate for effective sanitization/sterilization and troubleshooting.
Different training for different access levels to the system is taken into account and recorded on ZHM certificate of attendance. Action options and limitations for the End-User, which are diversified according to the access level, are cleary highlighted during training.
Validation of a pharmaceutical systems implies careful verification of functional and design specifications, to make sure that the final product meets all regulatory standards. ZHM standard validation package includes:
- INSTALLATION QUALIFICATION The documented verification of the system design is achieved by checking the as built equipment versus the design specification. IQ protocols include as built drawings, part lists, electrical schemes, software documentation. Our IQ protocols provide easy-to-fill check lists.
- OPERATIONAL QUALIFICATION The documented verification of the functional design is achieved by checking functional data against the functional specification. OQ protocols are conceived for easy recording of critical parameters and provide full support for effective system validation.
Our Customer Service provides effective after sales assistance, focusing on quick problem solving. The direct communication with our Customers and the full traceability of all system components enables us to easily detect the problem cause and to suggest the most suitable corrective action. Teleservice can be also configured on ZHM systems to ensure quick feedback by our Automation Dept. Special care is given to safe remote access policy for compliance with 21 CFR PART 11.
Applications
Our know how, our experience & equipment apply to:
BIOPHARMACEUTICALS
•Sterile Manufacturing Facilities
•Clean Utilities: Compendial PW, WFI and PS generation, storage & distribution
•Formulation & Solution Mixing plants
•Large and small volume parenterals production
•Complete bags and bottles technologies
•CIP/SIP systems
LABORATORIES
•Water systems
HOSPITALS
•Water processing systems
COSMETICS
•Preparation Plants
•Process water technologies
•Filling lines
FOOD & BEVERAGE
•Water systems
•CIP/SIP systems
POWERSTATIONS
•Customized water treatment systems